First off, we only choose the best cores to
rebuild - the rest get scrapped. We know that the best cores make the best engines,
and with our huge inventory of cores we can be very selective as to which cores get
rebuilt and which ones don't.
Once a core is selected, it undergoes careful inspection
for cracks, wear, and heat stress. If it passes the inspection, it is then disassembled,
cleaned, stripped to bare metal, and precision measured for specifications. If the
engine specs OK, it's on to the machine shop for precision machining.
All machine
work is done to exact tolerances, and all measurements are triple checked before
re-assembly. The assembly process is a painstaking procedure done entirely by hand
(not on an assembly line). All engines are assembled in climate
controlled clean rooms by certified engine technicians. During assembly all machined
surfaces are measured once again for accuracy.
Once assembled, each engine
undergoes dyno testing for compression, leakdown, oil pressure, and
leak detection using ultraviolet dye - and must pass
our final quality control inspection checklist. If everything checks
out, the engine is crated
in a custom wooden crate to prevent shipping damage and each package is insured at
full value in the unlikely case of a mishap in transit. |
The following list shows all of the new parts included in every rebuilt engine:
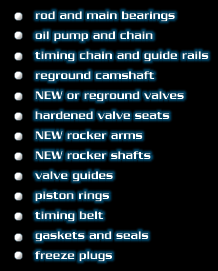
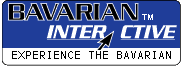 |